If you are like most engineering companies in the manufacturing industry, then you pride yourselves on being innovative, customer-focused, and cost conscious. However, being the latter also means you have a modest budget to spend on process improvements each year. Consequently, you’re always looking for ways to get the most out of the technology that you already own. Well, if your engineers are in need to getting accurate part costs (without a lot of effort, of course) and they already use Solidworks® Premium or Professional for design software, then they should also be taking full advantage of the powerful Costing module that is built right into the product. If you don’t believe me, just go to the “Evaluate” ribbon tab and look as far to the right as possible for a button labeled ‘Costing’. Solidworks® has done a really nice job of leveraging its inherent knowledge of the part that you just designed and automatically matching up the features with the associated manufacturing process to produce it.
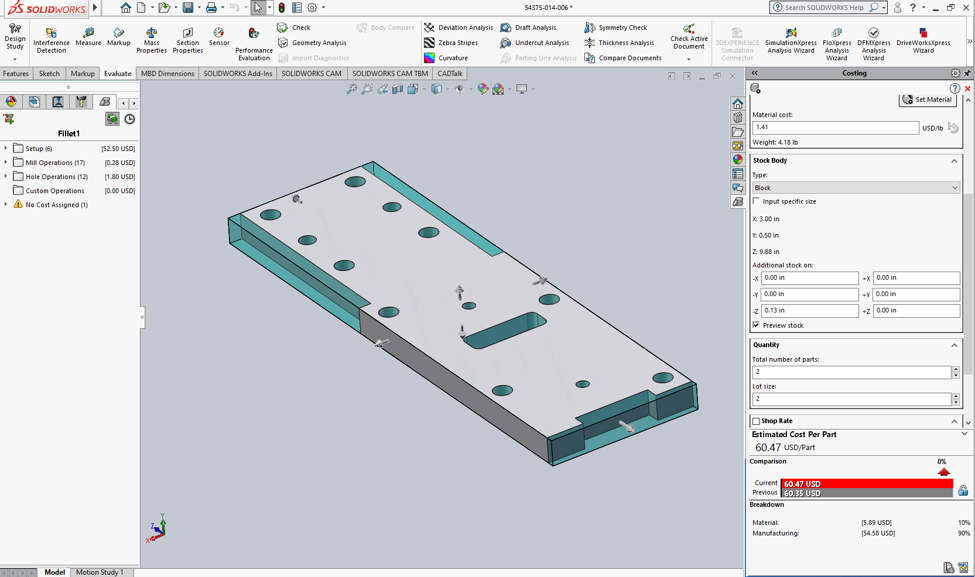
It supports processes such as milling, drilling, turning, 3D printing, welding, profile-cutting, casting, saw-cutting, and some others. Each of these machine types can have different cost rates for labor (and the machine itself) as well as its own default load/unload time & operation setup times, which is critical in determining an accurate per-piece part cost. One of the most attractive parts of this costing module is that comes with a pre-populated template of typical material costs and operation/labor rates for each process, which quickly gets you an initial “ballpark” estimate of your part cost. There is a template for both English and Metric units, and Solidworks® will load a different costing template depending on whether you have a multi-body part, a regular part, or a sheet metal part. For example, the cost template for a multi-body part will have machine processes for welding and sheet metal parts will have a cost template containing profile-cutting, bending, anodizing, painting, and inspection.
The figure below models the operation/labor component of milling cost:
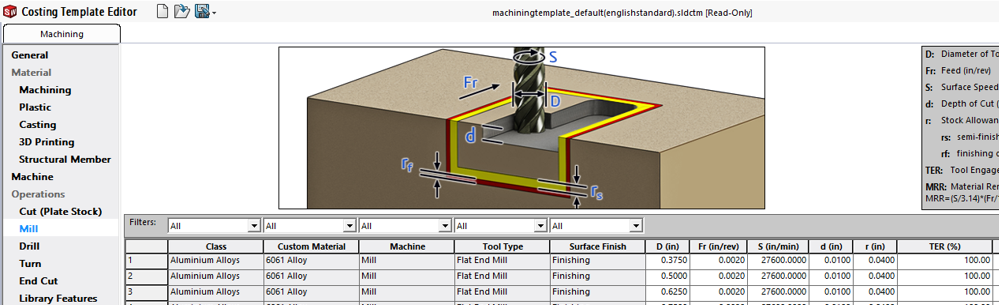
You can easily tweak any of the values to follow standards in your shop, for achieving even better estimated costs. Another benefit worth mentioning relative to machining processes, is that you can easily add stock on desired edges of the workpiece that you know are needed for end-milling (or facing on a lathe) to achieve a tight-tolerance requirement. Solidworks® displays the material to be removed in a blue-green color making it easier to visualize this (see first figure), and consequently adds the extra cost for the machining time needed.
For the sheet metal fabricators, there is plenty capability to capture the cost for laser-cut & bent parts using the sheetmetal costing templates for common material types (aluminum, steel, copper, and titanium alloys), as well as welding costs for multi-body parts. To give an example, a sheet metal part that is made of 22 gauge stainless steel with 8 standard bends and 10 hems, Solidworks® will automatically recognize that the material should be cut on the laser (because of its material and thickness), and detects the types of bends and uses the associated cost for the standard bends versus hem bends. The figure below shows the detail of the different operations on the left.
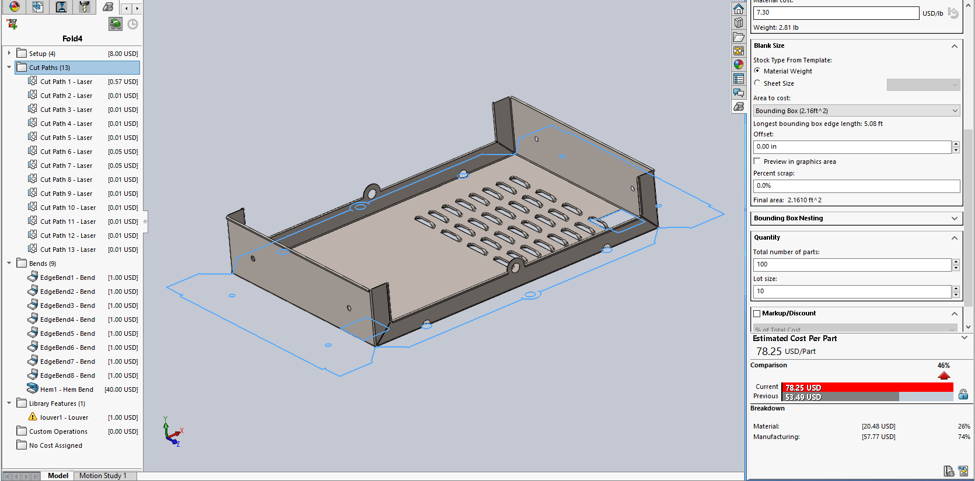
Obviously, for irregular-shaped sheet metal parts, you can achieve more accuracy on the material cost by running the part(s) through a nesting software, but Solidworks® will give you the conservative bounding-box material cost (with an option for loss of scrap %), which is typically sufficient for engineers designing mostly rectangular shaped parts.
This cost estimate that is calculated can then be added to your current list of custom properties, and even be read into the appropriate place in the item master record of your company’s ERP system. And you could quickly become your cost account’s new best friend.
In summary, no matter the type of part you are designing, Solidworks® has a robust, built-in tool to get you “well inside the ballpark” for a manufacturing part cost estimate. So when that vendor comes back with a price that sounds way too high, you can do your own cost study and reply to them with the cost breakdown report that you exported from Solidworks®!
CADTALK ERP transforms data from Solidworks® into manufacturing bills of materials, routings, items, and additional data inside your ERP system. You may also be interested in CADTALK NEST for connecting data from popular nesting layout applications with your ERP application. Want to learn more? Request a personalized demonstration.