While the benefits of connecting CAD systems with ERP platforms are clear, there are common concerns that keep many companies from spending the money on a potential solution. Let's explore three major questions that we’ve seen over many years here at CADTALK and why these perceived obstacles might be easier to overcome than you think.
1. IS OUR DATA GOOD ENOUGH?
Perhaps the most common concern manufacturers face is whether their existing data is "clean" enough for automated integration. Many engineers and managers worry that the quality of their current data may not justify the investment in integration software.
CADTALK CEO Scott Brickler offers a refreshing perspective on this, saying, "A person is probably [manually transferring data] today... and if there is enough information for them to decide how to do that, there is probably enough information for a software to give you some kind of benefit."There's probably enough information for a software to give you some kind of benefit.
Scott Brickler
CEO
The very nature of these systems enforces a certain level of consistency and discipline in data management. While your data might not be perfect, it's probably good enough to start seeing benefits from automation.
Interestingly, the relationship between data quality and integration often works in reverse. Rather than cleaning up all your data before implementing integration tools, having these tools in place tends to help point out and correct data issues. The software can provide the framework needed to understand what corrections are necessary, making the improvement process more focused and efficient.
2. ARE WE TOO DEEP?
Many companies balk at the perceived effort needed to implement integration systems, fearing it will take a massive upfront effort to clean up historical data and documentation. This misconception often stems from a “sunk cost fallacy.”
Picture this, you’ve already invested countless hours and potentially hundreds of thousands of dollars in your current system or process. And even though your current system doesn’t work great, it would be silly to spend more time and money to transition to something better, right? Wrong! Change for the better is just that… change for the better.
The time and money you’ve already spent on your system is a thing of the past. You shouldn’t let that affect your decision making today. Rather, take what you’ve learned and use it to make better, more efficient decisions.
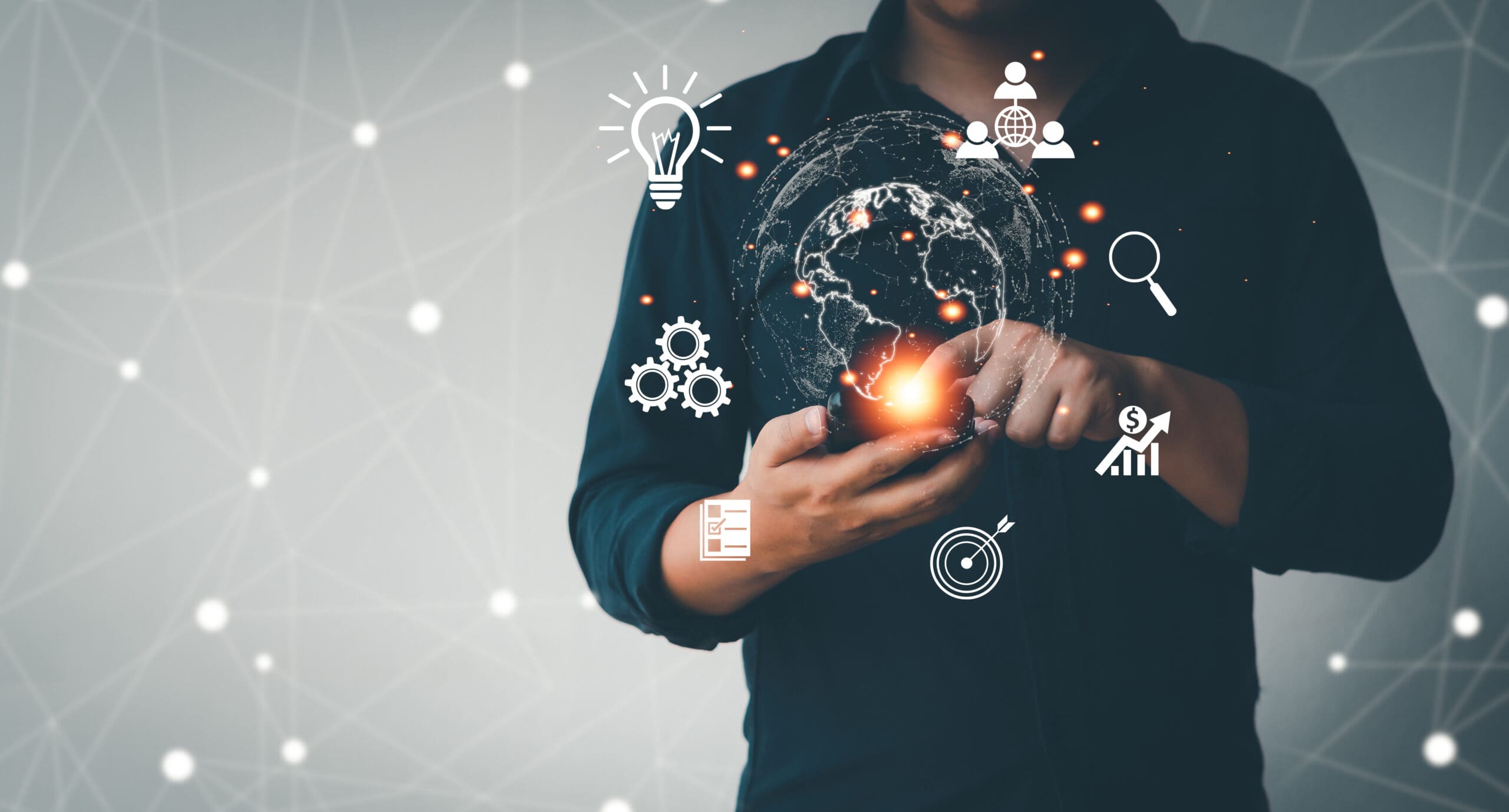
3. DO WE NEED TO CHANGE OUR CURRENT WORKFLOW?
A related concern is that implementing integration will force dramatic changes to existing workflows and processes. Many companies envision needing to completely reimagine how their engineering and manufacturing teams work together, thinking that it must be an “all or nothing” type of decision.
However, the best path forward is often to keep current workflows initially, just with automation in between.
This approach provides several benefits:
- Teams can continue working in familiar ways
- The only change is reduced manual data entry
- No need to retrain staff on new processes
- ROI is immediate through time savings
- Future process improvements can evolve naturally
A simple first step is to ask yourself, “What would it look like if I just added automation where manual data entry currently exists?"
Trying to pack too many process changes into an implementation is often a recipe for failure. Instead, focus first on automating existing workflows to free up time, then use that extra capacity to gradually improve processes based on real-world usage and feedback.
Successful change management isn't about making dramatic overhauls but about implementing small, manageable changes that compound over time. Each small improvement frees up time and resources that can be reinvested in further enhancements.
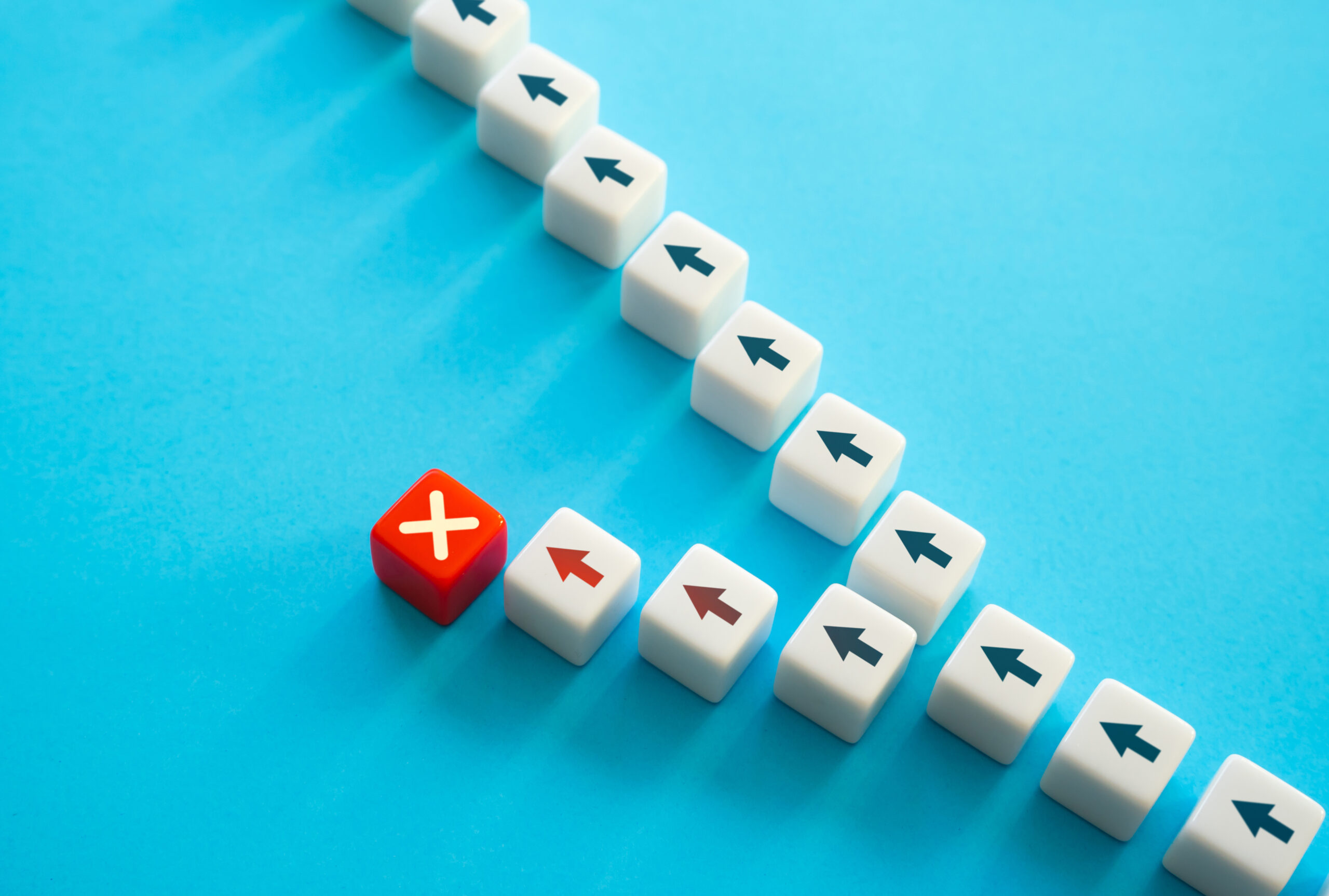
Moving Forward
Don’t make “perfect” the enemy of “good” when it comes to ERP integration. Rather than waiting for ideal conditions or trying to solve every problem all at once, companies benefit most from taking an iterative approach. Start with the basics, automate what you're already doing, and build from there. The path to successful integration doesn't require having perfect data or processes from the start; it just requires taking that first step forward.
SCHEDULE A CADTALK DEMO
Ready to see what CADTALK can do for your business? See it in action!