Manufacturing companies that do in-house metal fabrication are all too aware of how many CAD/CAM nesting software solutions out there in the market today. CAD/CAM nesting software is a highly competitive, niche industry where the product must possess a strong combination of CAD system integration, user-friendliness, powerful automatic nesting, efficient & safe tool-path functions, robust machine post-processors, batch/automation, and be capable of ERP integration. The immense value of the last item will be the focus of this article.
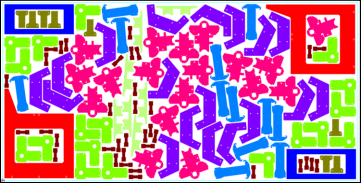
Figure 1 Example automatic nest of 9 different irregular-shaped parts at various quantities.
CAD/CAM nesting solutions fall into one of two categories: Third-party software & OEM-developed software.
Third-party systems are designed to work with many different machine brands and types, and include names like SigmaNEST, Lantek, Radan, JetCAM, PEP, Metamation, Alma, TruNest, Striker, NCell, and METALIX. There can often be partnerships between third-party vendors and machine builders, but they are separate companies which is an important distinction.
In the other corner, you have OEM-developed nest programming software where the same company that builds the machine also develops the software, with the prime goal of optimizing their own machines(s) to the fullest. Examples of OEM-developed software include TruTops (TRUMPF), BySoft (Bystronic), ProNest (Hypertherm), AP100US (Amada), Columbus (ESAB), CADMAN (LVD Group), FlowNest (Flow), and IntelliMAX (Omax).
Each of these 2 categories of software has its strengths and weaknesses, and every manufacturer/fabricator has their unique functional requirements and budgets – which is a big reason why so many choices exist.
When we talk about different machine types, it usually means:
· Laser
· Waterjet
· Plasma
· Oxyfuel
· Router
· Knife
· Turret punch
· Combination machines (punch + laser, punch + shear, machining + plasma)
To make matters more complicated for the software makers, some machine types can have advanced features such as a bevel-cutting, inkjet marking, multiple cutting heads, precision hole cutting, programmable clamps, special punching operations, sheet loading/unloading devices, robotic part removal, and the list goes on. All of which requires the software to have robust functionality to support such advanced features, not to mention staying up to date with the machine’s CNC controller (seen in the image below). So, as you can imagine, choosing the right software vendor is an important decision to an organization.
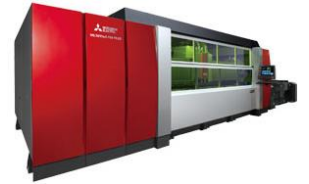
Figure 2 Mitsubishi 3015eX-F Fiber Laser Cutter
Regardless of what package your company has, you should never have to settle for having little-to-no integration between your nesting software and your ERP system. If you feel that your organization’s software has limited ability in this area, then contact your vendor and make sure that is the case. Do not just take someone else’s word for it. If it is capable of “integration”, then determine whether you own the prerequisite modules for doing such an integration and what the associated costs are. Lastly, do a little homework (or get a demo) to make sure it is a configurable and fully automatic platform that supports “bi-directional integration” at various points along your workflow.
It is important to understand the benefits of having a deep integration between your nesting software and your ERP system. Here are the top 9 benefits:
1. Eliminates time-consuming dual entry of part order data, reducing the possibility of human-error, ensuring that the right parts and quantities are being nested according to the latest scheduling information.
2. Can improve the speed, accuracy, and consistency of part cost estimates and material- labor allocations.
3. Assist design engineers with DFMA efforts by doing scenario nests.
4. Dramatically increases the speed that part orders hit the floor.
5. Throw away less raw material because you are more easily able to combine orders from ERP (onto the same nest) that use the same material grade & thickness.
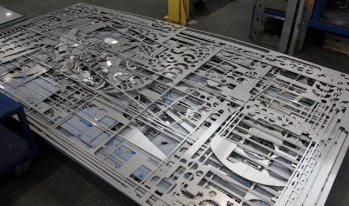
Figure 3 A typical sight next to profile-cutting machine
6. Ensure that the correct revision (or release) of a part is being cut.
7. Achieve more accurate raw sheet/plate inventory levels since the nesting software knows the actual amount of material being used.
8. Achieve more accurate job costing since the system knows precisely how much material is actually being used for each part order.
9. Reduce the amount of time your shop personnel spends on tedious job transactions related to nested parts.
Some of these benefits just described are quantitative and can be used to justify the investment, however, many of them are intangible benefits. These intangible benefits will streamline processes and positively impact your fabrication workflow, but at the same time can be harder to use for financial justification. Nonetheless, when presenting your cost justification/ROI to management, be sure to include all the benefits – tangible & intangible.
Now that we understand the wide range of benefits, let’s jump into 4 key areas where an integration between CAD, Nesting, and ERP can be extremely valuable:
A. Part Cost Estimating, Material Allocations, DFMA, and BOM entry.
Case #1: A design engineer needs to ensure that 4 large, irregular-shaped, side plates can fit onto a standard-sized sheet, to help minimize the consumption of material and reduce cost.
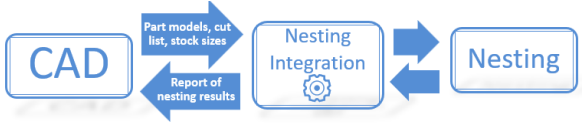
Figure 4 The diagram above shows the conceptual integration for DFMA that could solve Case 1.
Case #2: Another engineer is entering new items and BOM into the ERP and needs to quickly find out an accurate estimate of raw sheet material and the machine run time (per part) for the cutting operation.
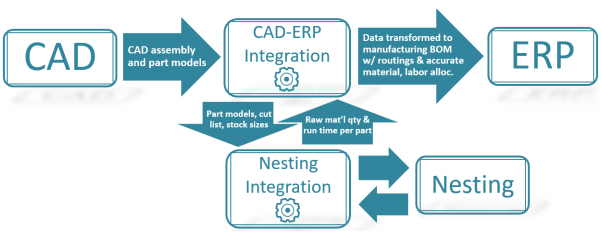
Figure 5 While more complex, the diagram above illustrates an integration that would solve Case #2 – potentially saving engineers an enormous amount of time and improving data accuracy in the ERP.
Case #3: Management is asking for a manufacturing cost estimate for a new prototype design based on a particular demand or lot quantity.
This case is perhaps the most complicated of the three, but possibly the most common for engineers. Certainly, it could be solved using cost estimating tools built into the CAD software or ERP system, but if there are many irregular-shaped sheet metal parts, then the material estimates will not be accurate since it isn’t nesting.
So, what is the answer here? A sophisticated approach would be having an integration very similar to what is described for case #2, but with a special emphasis on leveraging technology within the CAD-ERP integration component to determine routings and calculate operation setup/run times based on data available in the CAD models. A slightly different approach would be using Case #2’s integration in conjunction with a nesting software that has a more complete quoting-estimating engine built within it. This engine would not only accurately estimate material usage and labor for the cutting process, but for all other manufacturing processes.
B. Engineering change updates to sheet metal parts
When there are engineering change notices (ECN’s) with design changes that impact a flat pattern for a CNC machine, an integration can be critical for ensuring that the nesting software is automatically updated with the latest CAD part geometry.

Figure 6 This diagram shows a relatively simple data flow, however, the complexity is often found in the engineering department’s procedure for handing-off the CAD file to the nesting software.
C. Production/Job Order Queue for Nesting
When new job/shop order(s) are released to manufacturing, data on specific job/shop orders that must be nested are automatically sent to the nesting software’s own order management system. This is easily the most common integration found across the industry, so if you are not already doing this, then start working with your nesting and ERP software vendors to get this one done. It is easily the biggest bang for your buck.

Figure 7 It is implied that this type of integration is “real-time”, meaning that if any production requirements change (quantities, due dates, cancellations), the nesting software is immediately updated.
D. Machine Offload, Cut Verification, and Feedback to ERP
When a nested sheet of parts has been cut, there is usually a “cut confirmation” step that occurs within the nesting software. This is basically the ability to tell the system which CNC nest programs were cut on the machine. Some vendors offer kiosk-type applications specifically for aiding in the unloading & part sorting process and can also allow the operator to tell the system which nest was just cut.
The reason this integration can be complex is because there are typically multiple orders on the same nested sheet, and some of the orders may not even get finished on the same sheet. This means the integration must be able to handle the occurrence of job/shop orders on multiple nest programs.
This “cut confirmation” event should trigger an integration that communicates back to the ERP system the actual quantity of material to issue to specific job/shop orders. This quantity of material per job is accurate because it should be a calculation that amortizes the waste material from the nest across the parts using a weighted ratio. A weighted ratio is used so that the big parts on the nest take a “bigger hit” of the scrap allotment, while the small parts take a proportionally smaller hit of the scrap.
Additionally, this same integration should execute the transaction(s) to close the cutting operation on the job/shop order routing, assuming the required quantity of parts have been cut. This transaction can happen with or without the actual labor time.
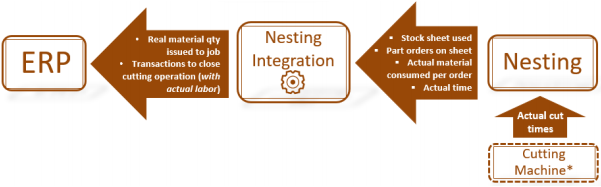
Figure 8 Diagram above shows the nesting data being fed back to the ERP.
* Collecting actual time from the machine depends upon either (A) the machine is already utilizing an industry-standard communication protocol like “MTConnect”, or (B) the machine manufacturer offers an interface allowing for data collection (e.g. TRUMPF TruTops Monitor)
It is important to understand is that, in a lot of cases, the nesting software vendor will not have an off-the-shelf integration that directly connects to your ERP and does all the things you want. Of course, you will find that there are some exceptions to this, so if the nesting vendor claims to have an integration to your ERP system, be sure to have them demonstrate it. Nesting solutions that are integration-friendly, will have a generic ERP interface (or a batch language or even an API) upon which a sophisticated integration to your ERP can be built. The figure below helps illustrate the “integration bridge” concept. Once you have your ideal nesting solution capable of integration, then you have a few options when moving forward with your project:
1. Find an integration consultant (preferably the ERP vendor or a certified partner) to build the nesting integration, with close involvement from you.
2. Explore the capabilities of products in the CAD-to-ERP integration space which may have existing integrations to your ERP. A product like CADTALK Nest would be one example that falls into this category.
3. For larger organizations with an “Information Systems” department (containing business analysts and programmers), find out if they possess both the knowledge and available capacity to construct such an integration for you.
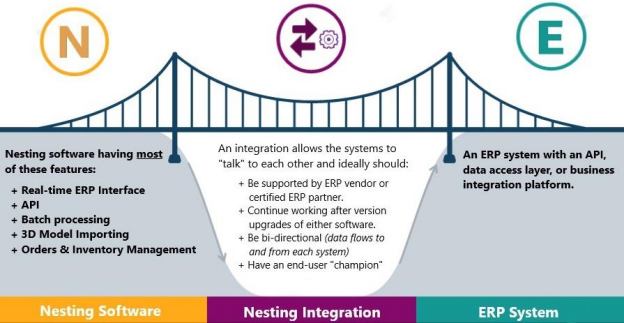
At this point, you should have a much better idea of what is possible with a sophisticated nesting integration, the potential value it has to your organization, as well as a bit of insight on how best to get started.