Implementing an Enterprise Resource Planning (ERP) system can often mean a lot of dedicated time, resources, and bandwidth at the expense of not only your management but also your company’s operations. Because of this, the beginning phases of software implementation can quickly become the center of attention. As a result, integration solutions, like CADTALK, may not even be considered until the second phase which risks miscommunication and forced errors such as over-engineering, duplicated efforts, and increased expenses due to lost automation opportunities.
Over-Engineering
During the first phases of the ERP implementation process, decisions are made that often create more work for engineers once the company moves to a CAD integration solution. These mistakes occur because, in the beginning phases, assumptions are made about how the engineering to manufacturing hand-off will be implemented in stage two. Without involving the expertise of the CAD integration vendor during the initial rollout of the ERP implementation project, the opportunity for setting up the ideal workflow will be missed. This lost opportunity will cause engineers to make assumptions that result in unnecessary changes to the design process. These misconceptions will result in more work for overworked engineers. This situation will lead to an increased engineering expense and longer lead times. To avoid this loss, it is critical to involve the CAD integration solution from the beginning of the ERP implementation process. By urging this investment from the start , it allows ERP implementation and automation software solutions to do exactly what they’re meant to do, i.e. produce greater efficiency and visibility into the business.
Duplicating Efforts
A common misconception with a CAD integration is that the CAD data must match the ERP dataset, which leads to unnecessary duplicated data on the engineering and manufacturing sides. The CAD Engineering Bill of Material (EBOM) and the ERP Manufacturing Bill of Material (MBOM) are different, yet some assert that engineers should insert information or data into their models for the integration to succeed. Oftentimes, this assumption remains incorrect considering the majority of the manufacturing process can be inferred from the model itself.
These beliefs are presented far too often when assessing both the software implementation and integration solutions which results in duplicated efforts on behalf of the manufacturing engineer
or production planner. Incorporating the CAD integration vendor while implementing the ERP system allows for design and manufacturing to communicate much more effectively by sharing the necessary information while avoiding any duplications. This forethought results in a reduction of personnel costs, risk of mistakes, and fewer miscommunications that can lengthen and complicate the final product.
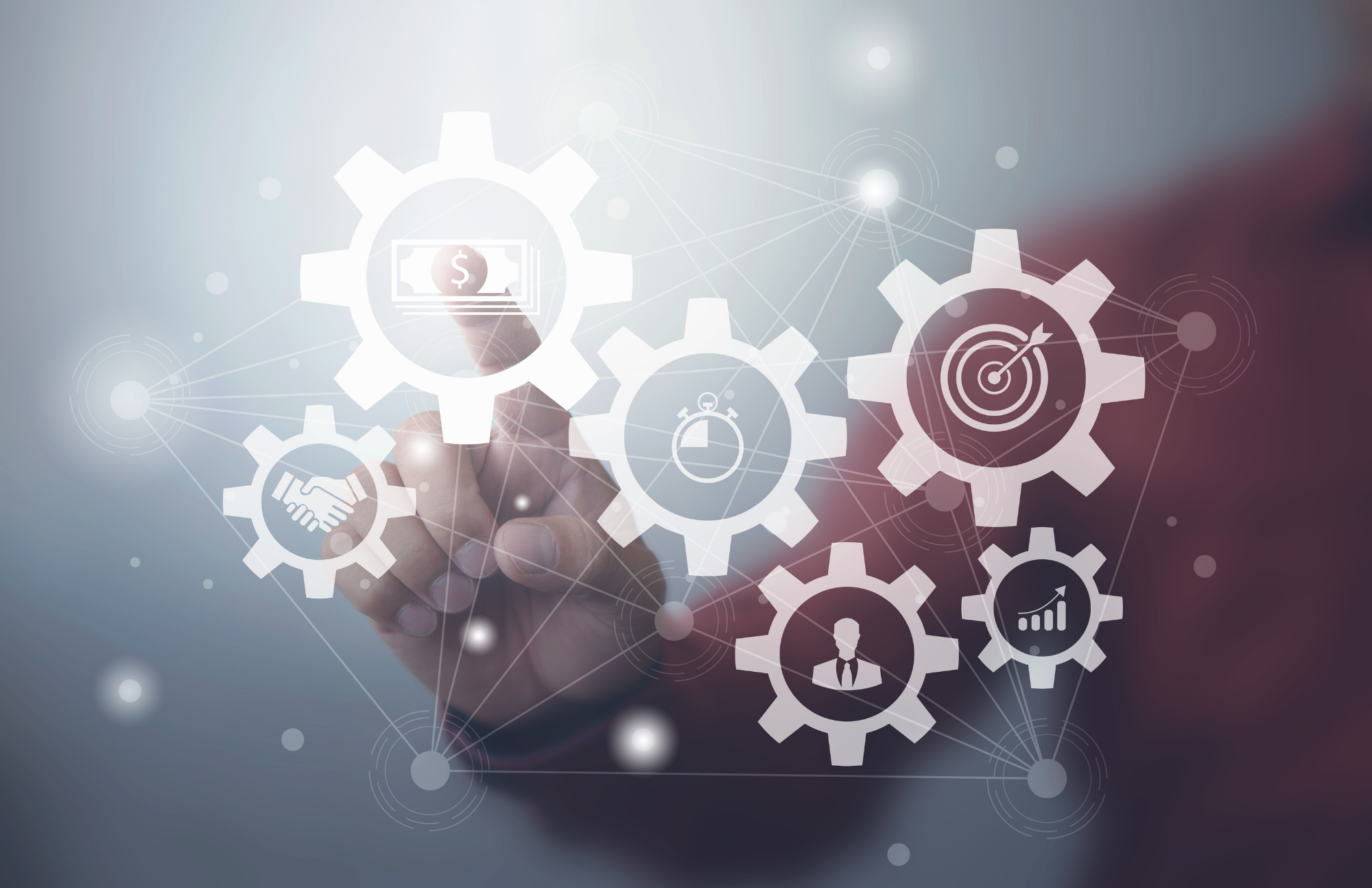
Lost Opportunity to Automate
While these aforementioned misconceptions and assumptions lead to doing too much, it also leads to genuine and major losses inside a company due to a loss of automation. This results in a multitude of issues seeing as automation improves efficiencies, reduces mistakes, and minimizes losses. By not taking into account and assessing all parts of the ERP implementation solution and CAD integration solution from the first phase of the implementation process, there runs a huge risk in a lost opportunity to automate. This is because, if you make a decision in the beginning phases of the process that eliminates the opportunity of automating something later on, there is no way to return to the beginning phases and retrieve the opportunity to automate. This lack of communication results in more manual processes which can directly lead to an increase in errors and a loss in time, production, and resources.
To schedule a confidential consultation or learn more, email info@cadtalk.com.