Selecting the right Enterprise Resource Planning (ERP) system is one of the most consequential decisions a manufacturing business can make. It's comparable to installing new plumbing or foundation work in your home.
A fundamental change that affects everyone and everything in your house. Or in the case of ERP, your business.
With so many stakeholders involved and each department having their own priorities, how do you navigate this complex decision effectively?
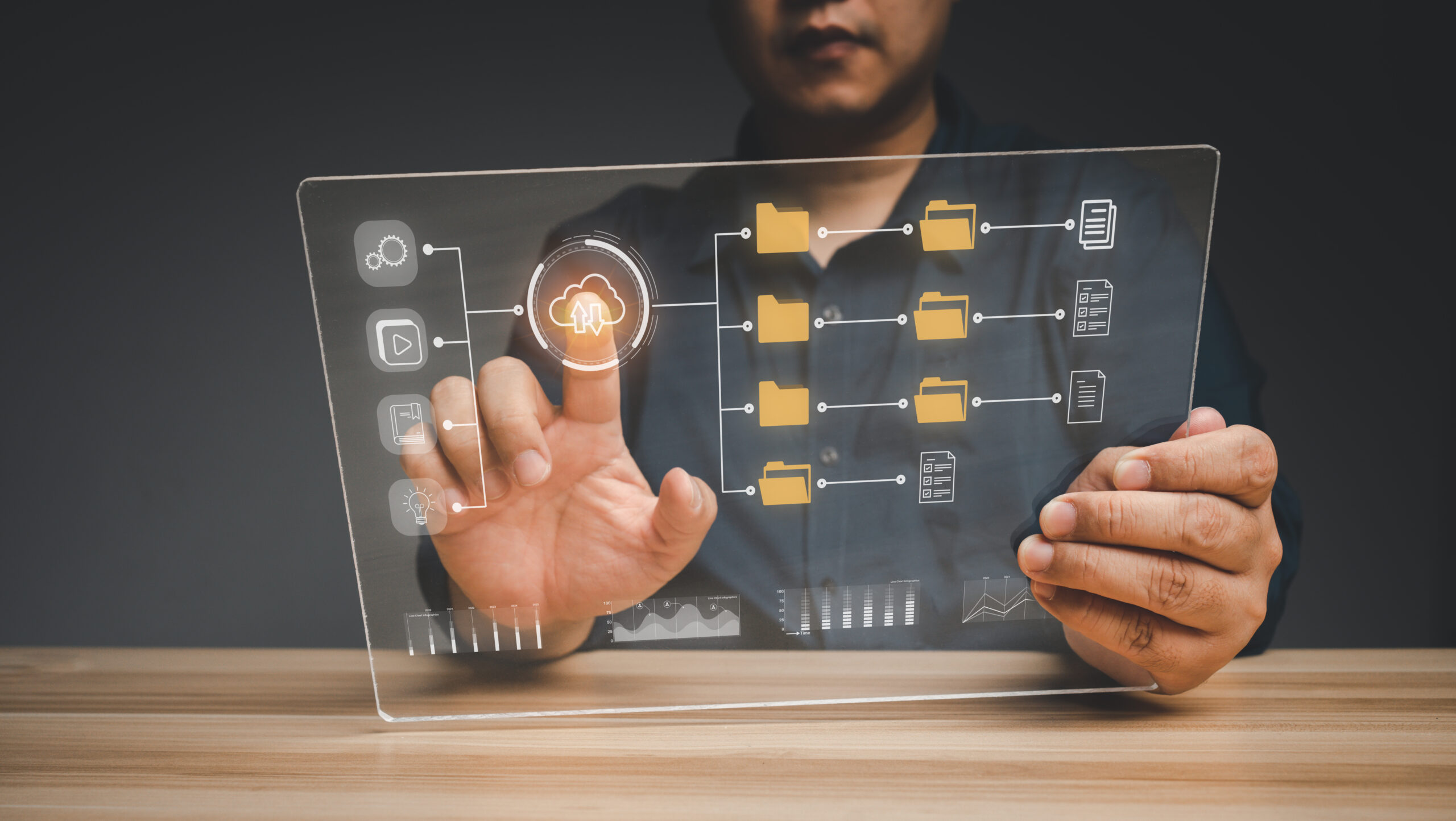
UNDERSTANDING THE OPTIMIZATION PROBLEM
At its core, ERP selection is a question of optimization. Every system has strengths and weaknesses, and no single ERP excels at everything.
You have to choose what you want to optimize for.
Much like the classic "good, fast, cheap – pick two" paradigm, ERP systems require trade-offs. You must decide what aspects are most important for your specific manufacturing operation.
Traditionally, ERP purchases are driven by CFOs, which is why many systems focus heavily on accounting functionality and financial reporting. This makes sense, as visibility into financials is vital for any business.
However, if you only optimize for accounting needs, you may compromise functionality in other areas like engineering, production, or supply chain management.
KNOW YOUR MANUFACTURING STYLE
Before evaluating specific ERP solutions, define your manufacturing style and requirements:
Defining your approach helps define what problems need to be resolved. Understanding your manufacturing approach provides the foundation for identifying which ERP features should be prioritized.
THE SIZE-COMPLEXITY CORRELATION
While there's a general correlation between company size and ERP complexity, exceptions abound. We've seen billion-dollar companies running on spreadsheets and $10 million businesses investing in enterprise-grade systems.
SCHEDULE A CADTALK DEMO
Ready to see what CADTALK can do for your business? See it in action!
The key factor isn't necessarily revenue but complexity.
- How many facilities do you operate?
- What is the diversity of your product line?
- Are you a global or local operation?
- What regulatory requirements do you face?
- How intricate are your manufacturing processes?
As operations grow, you typically need more robust functionality to manage increased complexity.

THE FLEXIBILITY FACTOR
One of the most critical yet often overlooked considerations in ERP selection is flexibility. Your business today won't be identical to your business tomorrow, and the system you choose needs to adapt to changes that will inevitably come:
- New manufacturing locations
- Product line expansions
- Regulatory changes
- Supply chain adjustments
- Technological advancement
- …Tariffs
The best systems balance fundamental functionality with configurability for future changes. Customization – once considered taboo in the ERP world due to upgrade difficulties – can be valuable if implemented strategically. The key is finding systems that allow customization while supporting upgradeability.
BALANCING COMPLEXITY AND USABILITY
It's worth noting that more complex systems aren't always better. For example, creating an invoice in QuickBooks is significantly faster than in SAP. The tier-one solution adds complexity to accommodate more sophisticated needs, but that complexity comes with a usability cost.
This is why templates or "stencils" can be valuable – they provide simplified paths for common workflows while allowing access to underlying complexity when needed. The ideal system offers both simplicity for day-to-day operations and depth for complex scenarios.
A MODERN APPROACH TO ERP SELECTION
Today's ERP selection benefits from modern tools and methodologies. Consider this tactical approach:
- Gather departmental insights: Survey each department about their biggest constraints and challenges.
- Find patterns: Look for common themes and pain points across departments.
- Focus on leverage: Determine which improvements would solve multiple problems simultaneously.
- Prioritize fundamentals: Identify which aspects of your business won't change and ensure the ERP manages these well.
- Build in optionality: Choose systems that allow for adaptation to meet future needs.
- Use AI: Along the way, utilize tools like ChatGPT to help distill information and make suggestions for which ERPs would be best suited for your needs.
This approach helps you make decisions based on organizational patterns rather than just departmental preferences.
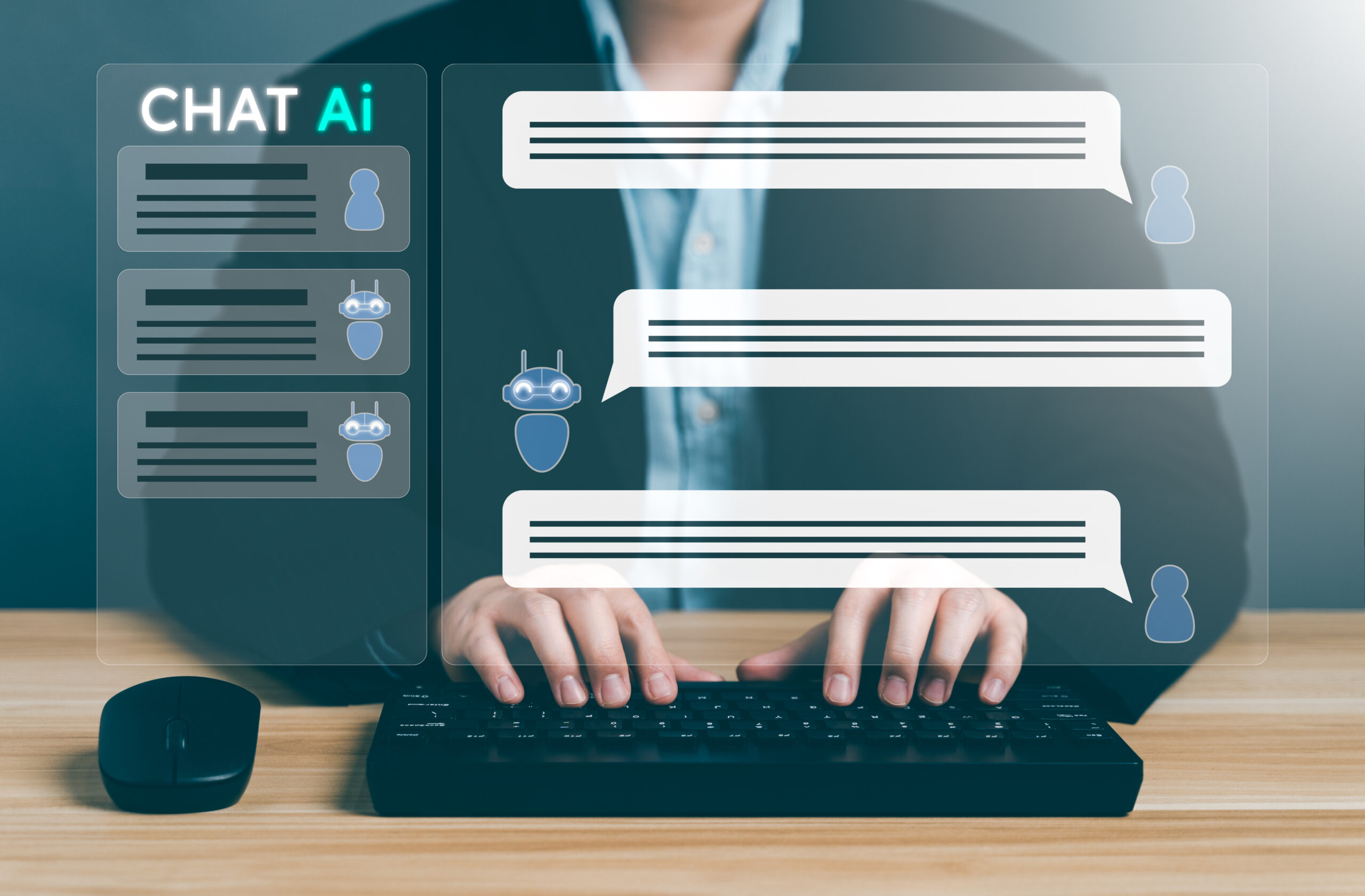
THE LOOK-AHEAD FACTOR
Manufacturing businesses need to think beyond immediate needs. What happens when you add a facility? Change materials? Expand globally? The "look-ahead factor" – considering how decisions affect future options – is crucial for ERP selection.
This is why flexibility and configurability matter so much. You might not know exactly what your business will need in five years, but maintaining optionality gives you the freedom to adapt when those needs appear.
CONCLUSION
The right ERP for your manufacturing business isn't necessarily the one with the most features or the biggest name. It's the one that best aligns with your specific manufacturing style, business complexity, and future needs. By understanding the trade-offs involved, prioritizing flexibility, and taking a holistic approach to selection, you can find a system that delivers value today while adapting to your business tomorrow.
Remember that this isn't just a technology decision – it's a business transformation that will shape how your organization operates for years to come. Take the time to get it right, involve key stakeholders, and focus on the features and flexibility that matter most to your unique manufacturing operation.